Environmental
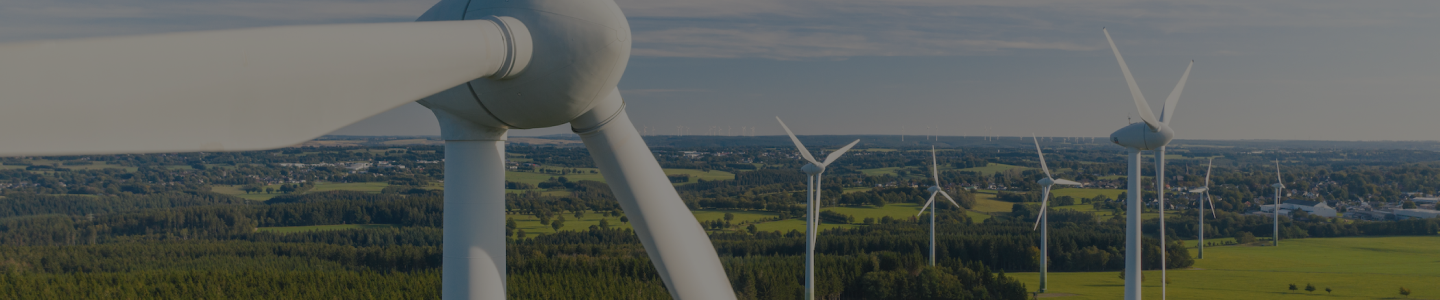
ENVIRONMENTAL ACTION
At Arcosa, we believe our established, environmentally-friendly product lines and strategic management of energy consumption and water conservation provide positive climate-related impacts. We remain dedicated to developing and implementing initiatives to support reduction efforts, which we anticipate will ultimately lead to direct climate improvement, improved financial returns, and organizational resilience.
STRATEGY
Arcosa’s sustainability strategy is to implement business-practical initiatives in high impact areas, with direct benefits for our plants and our people and far-reaching benefits for the places where we live and work. We are committed to collaborative environmental action at our sites to preserve and protect air, water, and land for today and for the future.
ENERGY
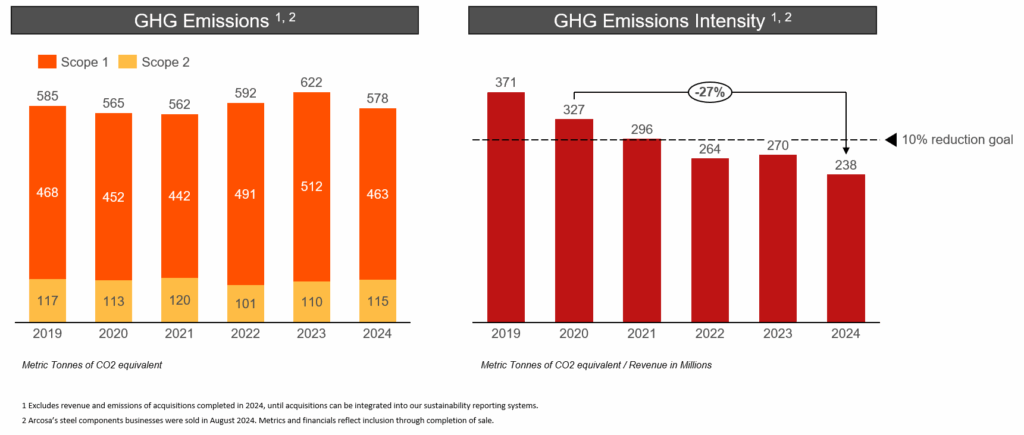
A major energy source for Arcosa’s Natural and Recycled Aggregates business is fuel for our heavy haul equipment. We continue to monitor and evaluate electrification options and are hopeful for technological advancements in that space over the long term. In the meantime, we look for alternative measures to move product, such as conveyor lines that have been installed at some facilities but, in many cases, haul trucks are the practicable solution. To manage and positively impact equipment-related emissions, our teams evaluate and plan for replacements to newer, more fuel-efficient equipment in line with replacement cycles. Our Houston, Texas-based Recycled Aggregates business works with the State of Texas to secure funding to support our equipment replacement plan. Under the program, the state aims to remove outdated vehicles and equipment from roads, job sites, and fields with the goal of cutting emissions and reducing impacts on the environment. Each year Arcosa plants participate in the program, and the equipment we replace contributes to improved fuel economy and overall emissions reductions in the business unit. For Arcosa’s manufacturing facilities, eliminating waste from production processes remains a high priority as we look to reduce emissions and stay competitive in mature markets. Arcosa views improvements in production efficiency as a large part of our emissions reductions plan and our manufacturing locations remain focused on energy savings initiatives.
Over the last two years, Arcosa’s Inland Barge facilities identified, researched, and implemented a project with far-reaching impacts to energy management and production efficiency. The team’s evaluation started with a need to improve a bottleneck on the production line as market demand began to drive increased production. They determined that upgrades to specific welding equipment would drive improvement within the line and realized improvements in multiple other areas, including:
- Production time reduced through more agile welding equipment
- Energy consumption lowered during production
- New power-save mode utilized when equipment not in use; reduced overall energy consumption
- Weld wire consumption optimized; improved operating cost and resource consumption
- Newer technology supports better diagnostics and preventative maintenance; improved downtime and costs
- Rework time and materials minimized
Arcosa and our facilities continue to look for ways to positively impact our world through practical, business-focused energy management initiatives. We are committed to improvements that allow us to continue to do the right thing every day, are supported by our wide range of stakeholders, and help us build a better world.
WATER
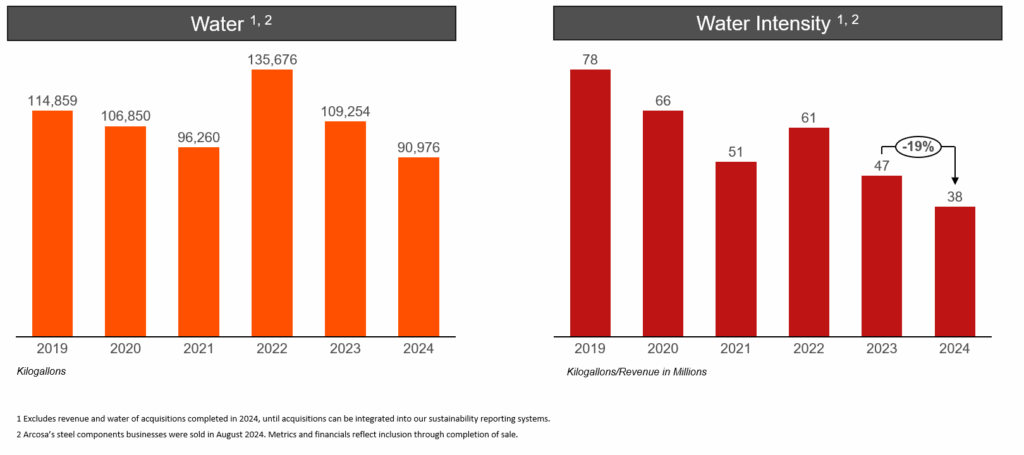
The employees of Arcosa Marine’s Tennessee barge manufacturing plant were abuzz with questions about the new orange bass logo that appeared throughout the plant early this year. During weekly safety briefings, an excited environmental, health and safety (EH&S) leadership team announced the refreshed, formalized Water Conservation Program. The program promotes sustainable water use through reduced water waste, enhanced water quality, and added focus on a culture of environmental stewardship. The orange bass, strategically placed next to water impact areas in the plant, is a visual reminder to employees that we are each responsible for the protection of water resources.
2023 in British Columbia, Canada saw a very dry spring and summer. For Arcosa’s Specialty Materials aggregates mines, which are heavily dependent on the use of collected surface water for production at wash plants, a dry season can negatively impact efficiency, make physical labor harder for employees, and halt the ability to produce material completely. To address depleted water reserves, our mine management team collaborated with Arcosa’s downstream Seattle, WA plant to reimagine the water-intensive crushing process from start to finish. Crushing is essential for forming materials into appropriate grades for infrastructure construction applications. The team spent time evaluating the many implications of water in the crushing process and how to eliminate the wash plant from the primary production line. After significant planning and vetting, the mine teams implemented a new process to crush “dry”, while still maintaining quality, sizing, and production rates.
The new process has numerous benefits, many intended and some unplanned:
- Reduces water requirements for crushing material; expect monthly reduction of nearly 1 million gallons of water.
- Reduces natural gas consumption in downstream production process to dry oversaturated material at sister site; reduces operating costs and scope 2 emissions
- Creates a cleaner site with less mud; improves cleanliness of conveyors, reduces downtime for blockages, and requires less manual labor for cleaning efforts.
- Improves labor efficiency through reduced materials handling.
- Improves material efficiency through reduced over-crushing, extending mine reserve life. Material loss has been reduced from 30% to nearly 0%.
The collaborative innovation and sustainability lens used by our teams for this project epitomize Arcosa’s commitment to build a better world. Arcosa is proud of the leaders in our organization and their continued efforts to implement business-practical initiatives in high impact areas, with direct benefits for our plants and people and far-reaching benefits for our communities and the environment.
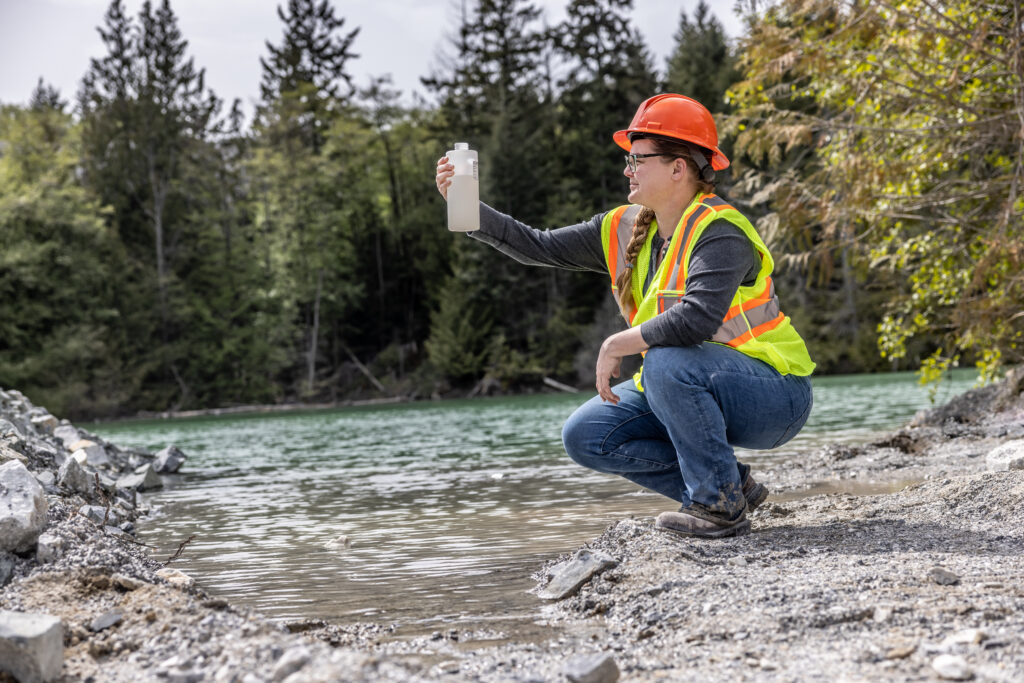
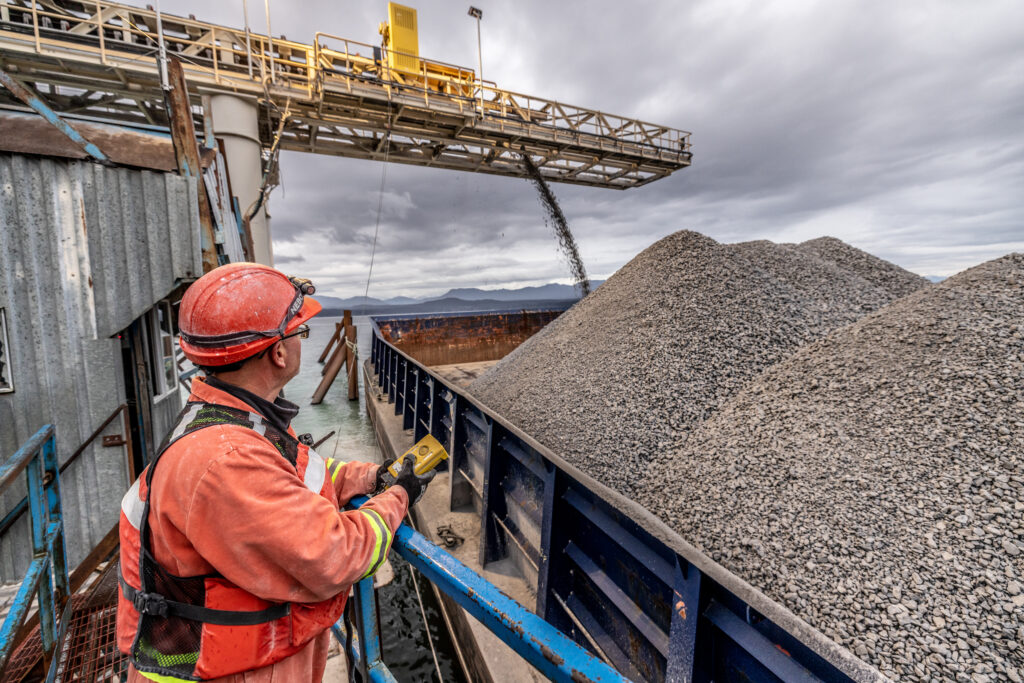